Laroche 3D-AIRLAY sheet forming for car industry
(Stand FE090, Inlegmash 2020)
The car industry has always encouraged its suppliers to develop innovative products.
Better insulation and lighter weight are the main requirements for fiber-soundproof parts such as floors and dashboard. Research shows that these results are achieved by parts with variable weight per unit area (g/m2).
A number of technologies have been developed. Most of them produce variable-weight gaskets by filling a 3D form with fibers and thermo-bonding. The need for individually molding every part is the problem with these technologies, considering that individual molds require fine-tuning and that one line can make only one type of parts at a time.
Owing to its solid connections with car industry suppliers, in particular, as a manufacturer of processing, mixing and air-laying lines and other equipment, Laroche has developed an alternate, more flexible technology
The technology makes a constant weight base using the known Flexiloft air-laying installation, and a second layer of the same-type or different fibers is applied to certain base parts. Once that is done, the 3D base is bonded and cut into pads that can be molded by standard presses.
It is a big advantage that one line could produce 2D flat pads at a high rate or various types of 3D pads with an easy change of recipe. There is no need for an individual mold for every part.
You can learn more about innovations of Laroche and technical features and additional capacities of the production line at Stand FE090, Forum Pavilion, EXPOCENTRE Fairgrounds, Moscow during Inlegmash 2020 on March 17– 20, 2000.
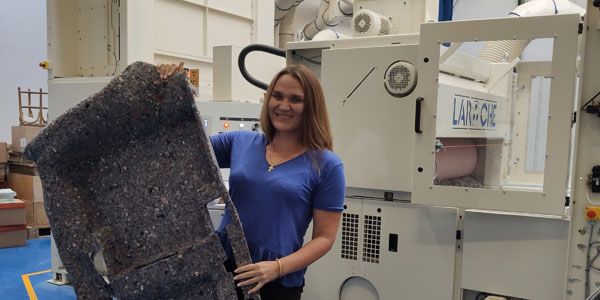